No one loses 25 lbs. overnight. The commitment to become Lean, whether in terms of personal fitness or business process, is very much the same. Both require a routine, or method, and practice.
In health terms, someone in great shape is said to be lean (low body fat) and are eating clean (protein and fruit, not potato chips and candy). Through exercise and routine, you reduce fat and build muscle. The value of being in great shape is that you are stronger and have more endurance, ultimately enjoying a better quality of life.
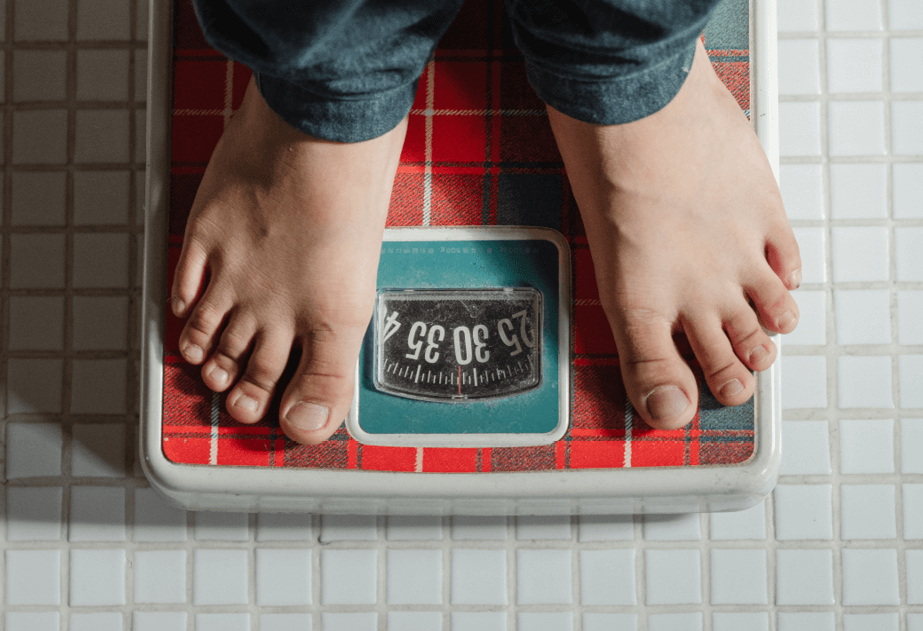
Lean Six Sigma is similar. It is a structured approach to reduce waste (fat) and define clean business processes (repeatable and measurable). It is the continuous exercise of studying your process to improve it and increase capability (muscle). The value of well-defined processes is higher throughput, better quality, reduced cost, and, ultimately, increased value to your customer. A better customer experience always translates to more sales. Happy customers buy more. Happy customers tell their friends through social media.
Business processes improved through Lean Six Sigma become repeatable and more efficient. A well-defined process also has well-defined measurement points. The real value of a well-defined process is that you can see its contribution to achieving your corporate goals. Like a series of connected gears, improved process performance becomes a leading indicator of your progress toward achieving those corporate goals, the lagging indicators. It helps you prioritize where to make investments that have the biggest impact.
What are the steps of Lean?
- Define the goals you want to achieve. These goals should reflect the “Voice of the Customer”, i.e. what does a great final product or service look like, from the final, end user’s point of view?
- Define the high-level process map. This includes identifying how the process gets started (Suppliers and Inputs), the steps that occur (Process), what it produces, and for whom (Outputs and Customers).
- Define the process boundaries. You will want to define, with a little more detail than the process map, the specific end-to-end sub-processes and steps that occur to create your product or service.
- Map out the Current State. Have the people that do the process lay out the flow of steps that actually occur, including decision points, hand-offs, and rework. Identify the key steps or decision points throughout the process and any current measurements you use to assess the work produced. This is your performance baseline.
- Identify waste. Walk through the flow, as a group, and challenge whether each step is actually necessary, meaning it makes a contribution to the development of the final end product for the Customer or it is absolutely critical for the process to continue. If it doesn’t meet either of those conditions, flag it as potential waste to be removed.
- Define an “Ideal” State. Take a breath and imagine how the perfect process could work if you didn’t have any constraints like time, money, or lack of technology. You are exercising both your common sense and your innovation muscles.
- Define your Future State. Revisit the Current State process flow. Remove any waste steps that are easy to remove. Verify what key steps or decision points would be a good place to measure and would provide some visibility to the status of work as it goes through the process. If you have an approach to remove wasteful steps with some workarounds or technology, map out how that would work, what process measure would be improved, and capture the workaround or technology as a potential improvement project.
- Prioritize your improvement ideas and engage the right stakeholders to validate the proposed approach and approve any investment required. Be sure to focus on the most impactful improvement ideas first.
- Implement your improvements, run the process and measure your performance. Make any adjustments needed and re-run the process. In short, wash, rinse, repeat.
Do you want good change?
The Japanese refer to the process of continually studying and improving processes as Kaizen. It literally translates to “good change”. Do you want good change? The steps are pretty straightforward. There are tons of resources to explain the details on how to do it. You could study that right now. Even with all this information readily available, what motivated you to take action and then keep improving?
Let’s go back to our weight loss analogy. Remember, no one loses 25 lbs overnight. There are tons of resources to explain how to do it. The benefits of being physically Lean are wonderful. Feel better. Perform better. Do more. Try new things that you couldn’t; do before. Live longer.
However, it is a rare bird that wakes up one morning and just starts their fitness program. Too many other things to do. It is uncomfortable. I’m tired.
A great approach to getting fit is to engage a coach. You still have to do the work, but they help you define goals. They design a program that meets you where you are in your current state. They get you started and work alongside you. It creates accountability. You enjoy measurable progress. Once the routine takes root, you can see the progress. Your confidence builds and you set new goals. You begin to entertain new ideas and new activities that you never thought possible.
Similarly, no business gets better all at once. Do you want good change? Good change often requires good guidance. Do you need a coach? While we can’t give you great abs, Keller Schroeder can help lead you toward continuous improvement. We have a practical methodology that you can immediately apply to a critical need, and that can develop into an enterprise program.
Do you know what you’ll actually be improving?
Like your first weigh-in, it starts with an understanding of your current baseline. To get that baseline, you will engage the people that actually work in that business process and document the current state process flow. Not the flow that everyone thinks they understand. Not the flow in the training manual created 6 years ago when the system was installed. You want reality. How the process got to be in the shape it is in is less relevant than how the process actually works day to day.
The objective? Eliminate waste, streamline the process so it flows smoothly, and doesn’t get clogged up in the middle. End result? Your product is delivered, at a good cost, with good quality, same or better than competitors, and meets the customer’s expectations.
If you have never assessed your processes for waste, and you are writing or buying software to enable your process, did you just automate waste? Yes, you did. If you have automated waste, and have never assessed your process doing a “value stream”, won’t you naturally just improve it over time? No, not unless some outside force challenges the way things get done. Why? Because it was a big investment to build the software, and, you have many other priorities and other processes you want to automate.
Additionally, in your organization, no one may be really measuring the process performance and you might not hear anyone complaining. That is a part of your culture, and companies tend to just “live with” these types of unseen challenges. In an unfortunate way, software automation contributed to the creation of bloated processes, siloed functions, and additional waste. What used to happen naturally, when the company was smaller, and when everyone all sat near each other, was that the staff were all dialed into the customer and the progress of each new sale. Now, employees sit at a computer to “feed the beast”, and, their “beast” doesn’t talk to their colleague’s “beast”.
The shame of it the entire situation? The best user interface doesn’t ensure the data you collect is consistent or complete so you can learn from it later. Won’t this hurt our business over the long term? It’s very likely. So, what do we do? While not a comprehensive answer, at a high level, prioritize your most critical processes, conduct a Value Stream Mapping of it, identify and eliminate waste first, then assess how automation can integrate all the systems and processes that create your product or service. Think about the data you will want to study later and design for that now.
Can we do that fast? Looking back to our weight loss analogy, let’s ask, “Can you lose 25 lbs by morning?” It is important to remember, just like dropping pounds, the key is to just get started and stick with it. You’ll feel better and live longer. If you would like a coach to get started, reach out to our Data Strategy Group and leverage their experience on all things “Lean.”
To hear more from Tom on Lean, check out this episode of our Technically Speaking Podcast Series
Written By:
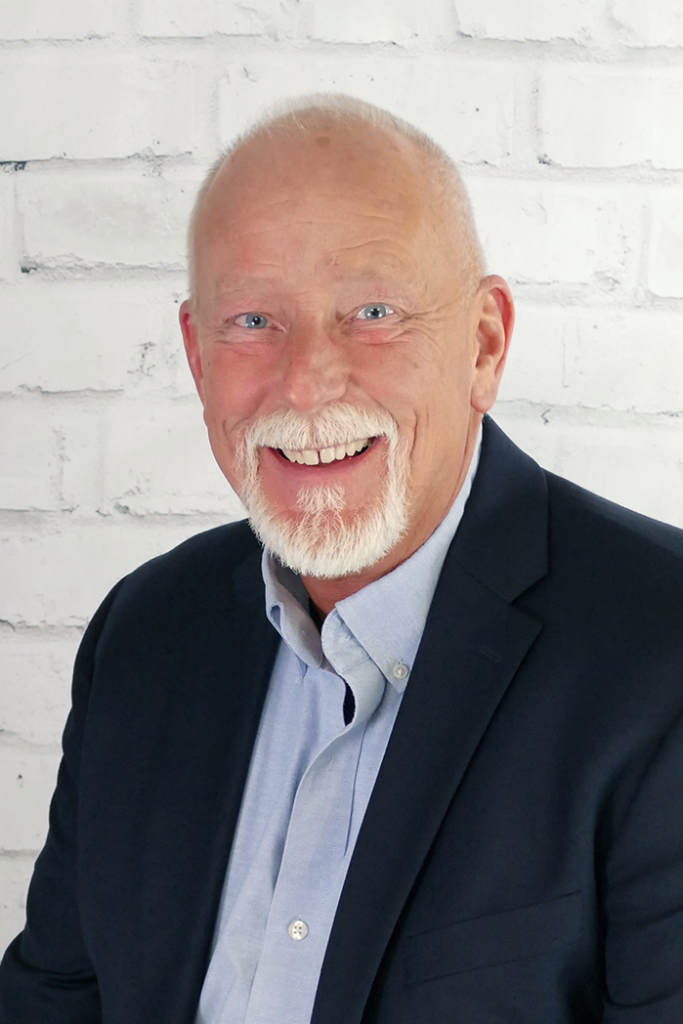
Tom Vargo
Vice President
Data Strategy Group